
When we talk about innovation in the field of modern textiles, a material called polyester high elastic 300D is gradually emerging. It not only has all the advantages of traditional fibers, but also has won high recognition in the market due to its unique physical properties and wide application.
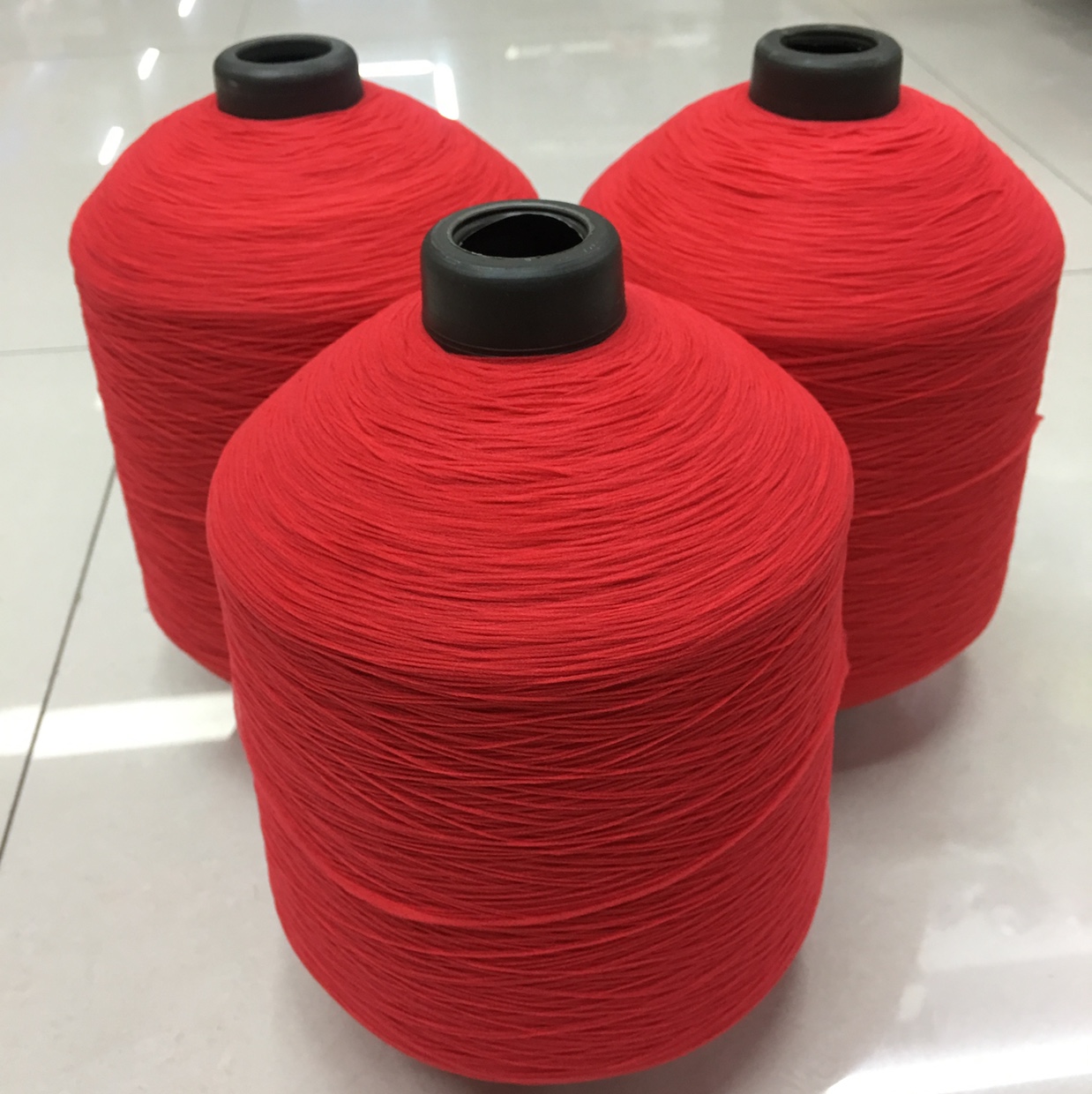
To truly understand what high-performance fibers are, we need to deeply understand the core advantages of polyester high-elastic 300D. As a synthetic fiber, its main component is filament yarn made of polyester, which is endowed with higher elasticity and stronger toughness through special stretching technology during processing. This means that even in the face of repeated pulling or complex environmental conditions, the material can still maintain the original shape and strength.
Why are more and more designers and manufacturers choosing Polyester High Elastic 300D? This is because this material has unparalleled advantages-first, excellent wear resistance, even if used for a long time, it is not easy to break; second, strong anti-wrinkle ability, making the finished product more flat and stiff and not easy to deform; third, excellent rebound performance, whether in sports clothing or outdoor equipment can provide a comfortable wearing experience.
In addition to the above characteristics, the practical application field of polyester high elastic 300D is also remarkable. From the slim pants launched by high-end fashion brands to functional underwear trusted by professional athletes, to industrial-grade protective clothing and other special equipment components... it can be found in almost every industry. Especially in the need to take into account the soft feel and strong support, such as hiking backpack shoulder strap or stroller seat cover and other fields is to show unparalleled value.
So how is such a high-quality fiber born? Simply put, it is through multiple precision processes to complete the entire production process. The first step is to extract raw materials from petroleum and form sliced granular substances through polymerization. Then these particles are heated, melted, extruded into continuous filaments and rapidly cooled and solidified to form them. Then, the primary filaments are arranged by mechanical means to significantly improve the mechanical properties. The last step is to adjust the thickness, density and other relevant parameters according to customer requirements until the expected standard is reached.
With the advancement of technology and changes in social needs, the research and development of new composite materials has become one of the important driving forces for the development of the industry. For star products like polyester high elastic 300D, the future is full of infinite possibilities. For example, we can achieve sustainable development goals by adding environmental protection factors to reduce carbon emissions; or try to combine with other advanced materials to develop more diversified solutions to meet diversified market needs, etc. In short, no matter how it evolves, I believe that this kind of technology with high efficiency and good social responsibility will continue to lead the trend!
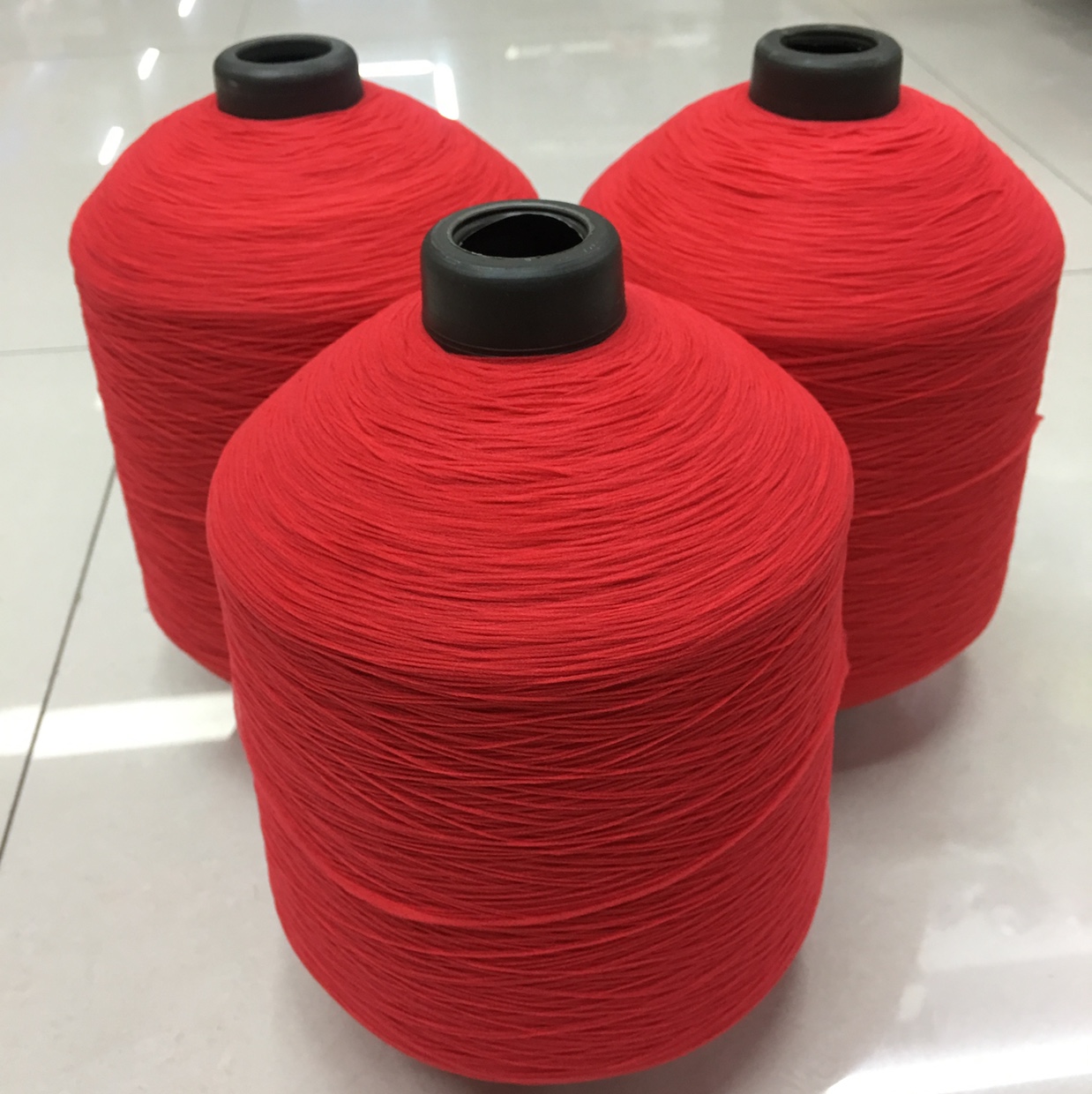